Know-how.
Harsh Environments
We can develop and optimize power converters to work at extreme temperatures (from -40°C to 220°C) and high shock and vibration levels. We use high temperature electronics technologies (such as SOI), but also industrial standard technologies (Si and SiC) for the best cost, temperature control and lifetime compromise. We master assembly and packaging techniques for temperature, shock, and vibration hardening.
Motor Control
We have developed and mastered our own simulation models for motors and inverters, our own control algorithms, and our own power stage designs. Depending on the application requirements, our motor controllers can be easily configured to select the operating mode: motor shaft position regulation, speed regulation, torque regulation if Field Oriented Control is included, power regulation or DC voltage regulation if the machine is in electric power generator mode. A variety of motor controllers are available, covering a wide range of power and voltage. We can customize an existing product to fit your requirements if necessary.
Power Supply
We have the skills to design your power supply: topology selection, galvanic insulation or not, analog or digital control, form factor, magnetic design, control algorithm design. Our experience in power electronics, magnetic components and efficient thermal management enables us to provide best-in-class power supplies and innovative, compact, and cost- effective solutions. Besides providing you with a range of off-the-shelf power supplies, we also design tailor-made solutions to best fit your needs.
System Integration
We investigate the effects on the system of each of our subsystem performances. To achieve these goals, most of our products are based on a digital core with CAN bus communication to complete performance monitoring, system configuration, real-time tuning of the converter or the motor driver control algorithm. At the earliest phase of the project, we are able to make a complete simulation model of the provided product and the related tool subsystem ensuring a better understanding of effective product performances and limitations.
Services.
-
Downhole Tool Architecture
We are highly experienced in downhole tools electronics for oil and gas wells. We can help you design your electronics architecture and write specifications for tool electronics. We provide feasibility studies to understand and size your needs in power supplies, motor controllers, control boards, and identify how all these elements can be implemented to meet your functional needs.
-
Modeling
Through Simulink, we model the electrical architecture, either entirely or partially. We can simulate your scenario and verify that the proposed architecture and equipment performance meet your functional expectations. Our simulations can include studies on HV bus stability, motor drive performance, power consumption, or any other critical point of your architecture.
-
Hardware Design
We choose the best topology to meet your requirements (performances, environment, form factor, and cost). We size the power components by calculation, simulate the HW (LT spice and PSIM), the control loops (MATLAB Simulink), and provide a footprint for the system (Solidworks). We provide an electrical and mechanical design that allows you to visualize the outcome of your product
-
Software Design
Depending on your requirements, our services may involve firmware and software developments. This includes code generation from Simulink, the C code development of drivers and communication stacks, the C++ development of the graphic user interface, or the HDL design of companion chips and mission-critical apps. Software design is done in-house by our developer team. This way to develop firmware is the most versatile way to do in the market. This allow to adapt the equipment behavior within limited development time and validation.
-
Prototyping
In-house prototyping allows fast, easy iterative work on the prototype for improvement and debugging. These capabilities include qualified personnel, CMS mounting, winding workshop, software design, and simulation.
-
Qualification
We test prototypes and validate expected performance according to a test plan that has been accepted by the customer. To ensure the reliability of our solution regarding specific environments, we qualify and validate temperature, vibration, shocks, EMI, radiation, lifetime, and thermal cycling
-
On-site integration
We provide necessary technical support and documented training courses to the team in charge of system integration.
-
Industrialization – Production
The production and testing facilities can manage the manufacturing of 10 products, up to 15,000 units a year. Boards assembly is done by one of our qualified sub-tier suppliers. Final integration, final tests, and burning test are done in-house.
-
Customer Services
We believe our role continues well after delivery and customer satisfaction. Our aftersales services team is always available to follow up with any of your inquiries and requests, converting power into confidence.
-
Obsolescence Management
Because some products and tools are maintained for decades, we support our customers in maintaining their equipment in operational condition. We track obsolete parts and make strategic stocks or to redesign a product with a newly available part.
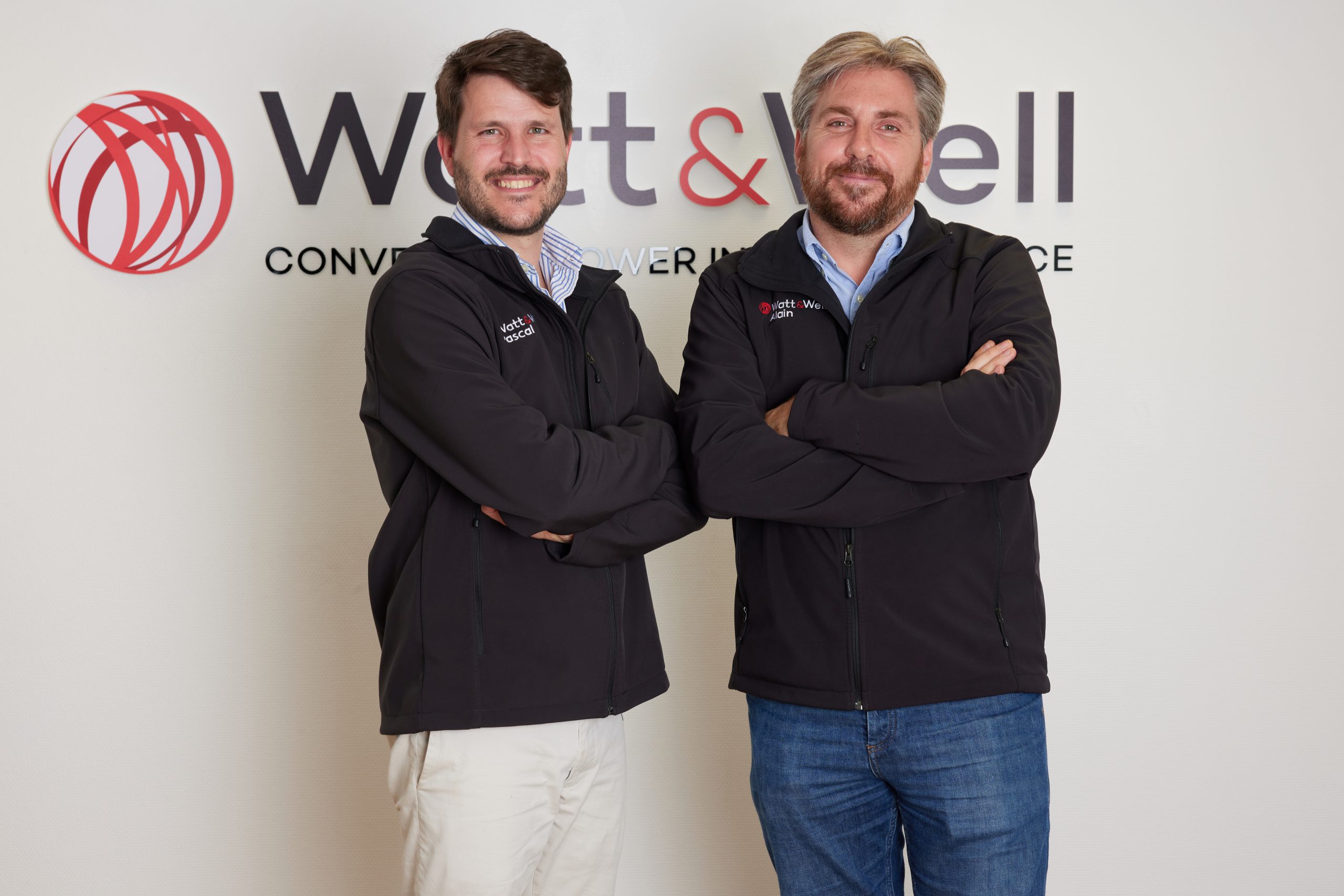
Let’s discuss your project. We are commited to answering you as soon as possible.